A few months ago we showed how the QC inspector job would get easier with the help of a mobile app.
Today we want to show how the right technology will allow quality control departments to be better organized and to cut lead times.
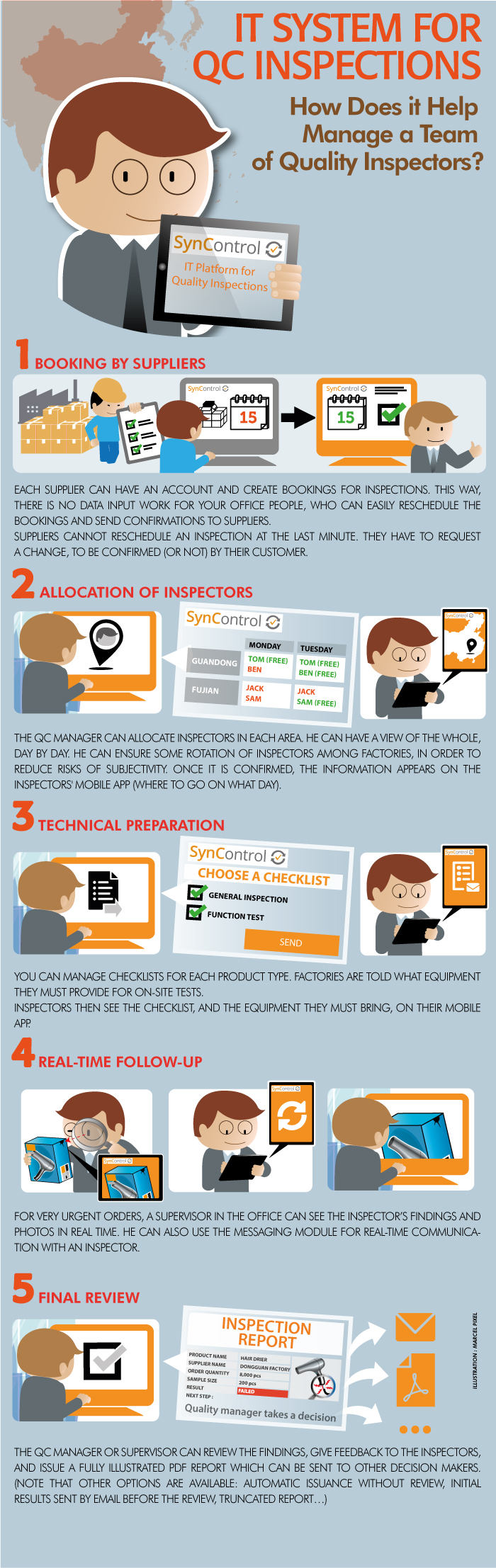
There are several ways technology helps.
Streamlining the booking process
Most procurement offices exchange emails and phone calls with factories to confirm the dates of upcoming inspections. Then they update an Excel file and share it (more or less) among their team.The most efficient is to link inspections to suppliers — in other words, to force them to book inspections. That’s what all big importers do, from my observations. If your suppliers are not cooperating, another solution is to pull the data directly from your ERP (or an IT solution that helps you
Optimizing the allocation of inspectors
What I saw in most quality departments is an Excel file that lists inspections (usually based on bookings from suppliers, as I wrote above). Inspectors are allocated based on their location and (usually) on their competencies.Ideally the QC manager would assign inspectors with a view over their workload (spreading the work more evenly among the team). He would also ensure inspectors are rotated – this is important to keep all parties careful and on guard.
The solution is to give a clear dashboard that displays this information visually. It would require several pivot tables in an Excel sheet, so it is seldom done.
Assigning the right checklists and specifications
A common problem is poor dispatch of information among the team. Design & engineering changes are common, rendering many files obsolete. Chinese manufacturers seldom have good document control, hence the need to be very vigilant on recent changes in specifications.A good IT system keeps track of changes in documents and ensure only the latest version is available to everybody. It also standardizes checklists and defect lists based on product types, for a gain both in efficiency and in reliability.
Communication between field staff and office staff
In my experience, phone calls to inspectors result in misunderstandings at least 10% of the time. Using Wechat is an improvement, but the ideal is for the office staff to be able to see what inspectors are doing in real time — to see the photos they have taken, the comments they have written, etc.This is possible once inspections are done on a tablet, with real-time synchronization of data. Add to this a simple messaging system, and inspectors become much easier to manage from a distance.
http://www.sunchineinspection.com/how-technology-will-support-quality-control-infographic/
Article Source:qualityinspection
No comments:
Post a Comment